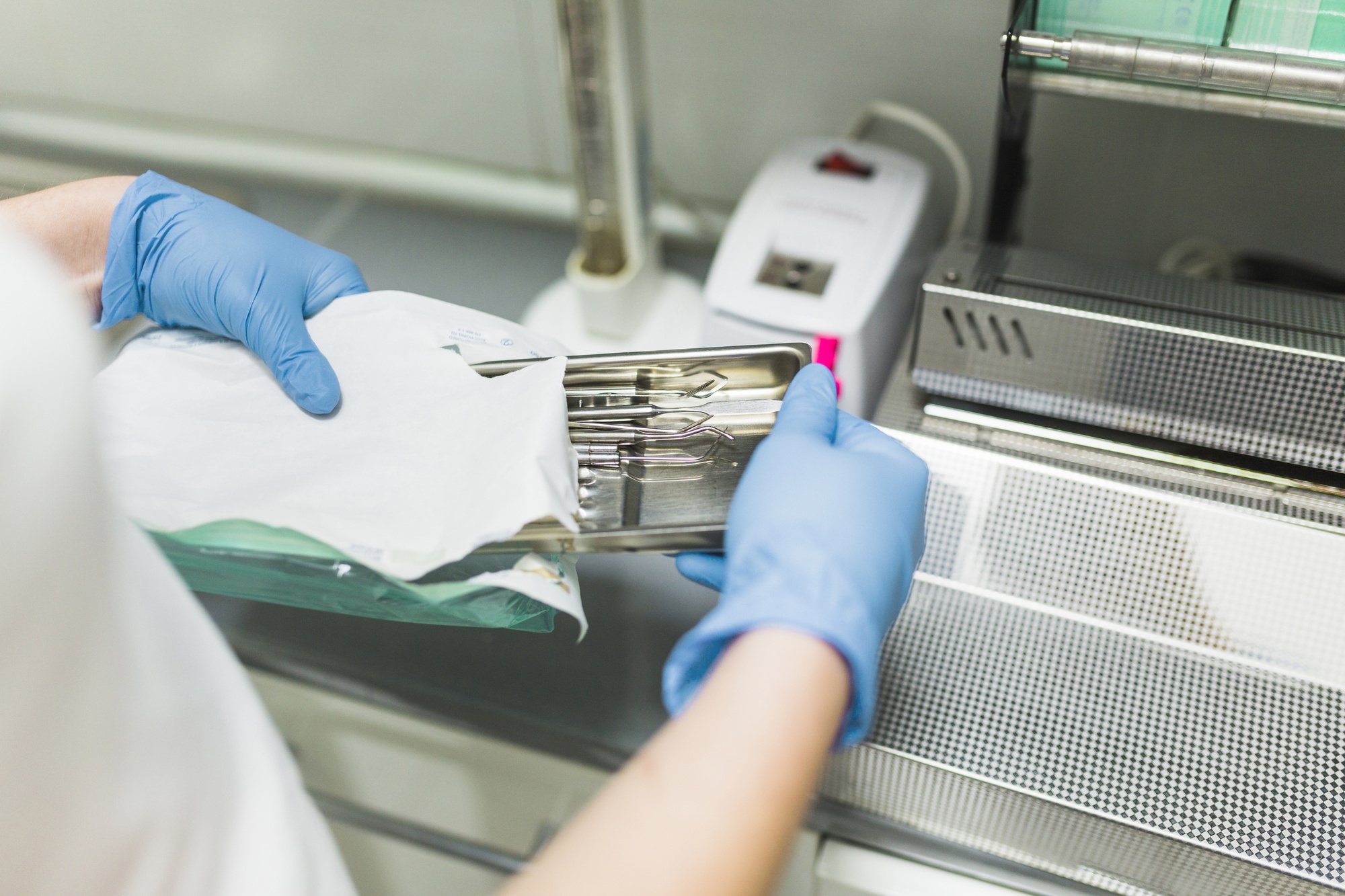
In the pharmaceutical industry, cleaning is more than just maintaining a spotless facility—it’s a critical component of ensuring product safety, regulatory compliance, and manufacturing efficiency. Clean environments directly affect product quality, patient safety, and brand reputation.
In this article, we will explore:
- What is cleaning in the pharmaceutical industry
- Types of cleaning
- Types of cleaning sampling methods
- Benefits of proper cleaning
Let’s dive in!
What is Cleaning in the Pharmaceutical Industry?
Cleaning in the pharmaceutical industry refers to the process of removing unwanted contaminants such as residues of active pharmaceutical ingredients (APIs), excipients, microorganisms, dust, and other foreign matter from equipment, surfaces, and manufacturing areas.
Pharmaceutical manufacturing processes involve sensitive materials, and even minute traces of contaminants can compromise the integrity and efficacy of the final product. Therefore, cleaning is an essential part of Good Manufacturing Practices (GMP) and is strictly monitored by regulatory bodies like the FDA, EMA, and WHO.
Types of Cleaning in the Pharmaceutical Industry
There are several types of cleaning methods used, depending on the nature of the product, equipment, and manufacturing process. Here are the most common types:
Explore a leading manufacturer of APIs.
With over 10 years of expertise, we ensure GMP compliance and provide reliable, high-quality solutions.
Level 0 Cleaning (Routine/Operational Cleaning)
Definition:
Level 0 cleaning is the most basic or routine cleaning performed during normal production operations. This cleaning level focuses on keeping workspaces, equipment, and surroundings tidy to prevent accumulation of dust or debris.
Purpose:
- Maintain general cleanliness during the production process.
- Prevent dust buildup or minor contamination during regular operations.
Example:
- Wiping down surfaces of equipment and floors during Bimatoprost batch production.
- Cleaning of operator shoes, doors, and frequently touched surfaces daily.
Level 1 Cleaning (Batch-to-Batch Cleaning)
Definition:
Level 1 cleaning is performed between batches of the same product. It focuses on removing visible residues and product buildup to prepare the equipment for the next batch of the same product.
or
It is the process of removing the gross accumulation of residue from the previous batch of the same product.
Purpose:
- Ensure no residues from the previous batch carry over to the next batch of the same product.
- Meet GMP standards for batch separation.
Example:
- Cleaning processing equipment after completing Batch 1 of Bimatoprost before starting Batch 2 of Bimatoprost.
- Includes cleaning of mixers, tanks, and pipes used in the production of the same product.
Level 2 Cleaning (Product Changeover or Deep Cleaning)
Definition:
Level 2 cleaning is the most extensive cleaning and is conducted when changing from one product to another (product changeover) or after extended downtime or maintenance.
Purpose:
- Prevent cross-contamination between different products.
- Perform thorough cleaning of all equipment and production areas.
Example:
- Cleaning after manufacturing Bimatoprost, before starting production of Travoprost (a different product).
- Includes disassembling parts, detailed equipment cleaning, cleaning of cleanroom surfaces, ceilings, and HVAC components.
Summary Table:
Level | When Performed | Purpose | Example (Bimatoprost) |
---|---|---|---|
Level 0 | During production | Maintain basic cleanliness | Wiping workstations during Bimatoprost production |
Level 1 | Batch-to-batch cleaning | Remove residues of the same product | Cleaning equipment after Batch 1 of Bimatoprost before Batch 2 |
Level 2 | Product changeover / deep cleaning | Prevent cross-contamination | Deep cleaning after Bimatoprost before producing another product. |
Types of Sampling for Cleaning Validation
Once the cleaning is performed, cleaning validation requires sampling to ensure no residues remain. Here are the two most common sampling methods:
1. Swab Sampling
- A swab is used to wipe specific areas of equipment surfaces to check for residual contamination.
- Effective for critical and hard-to-clean areas.
- Results provide quantitative data on residue levels.
2. Rinse Sampling
- The cleaned equipment is rinsed with a solvent (often purified water).
- The rinse is collected and analyzed for residual contaminants.
- Suitable for large surface areas and internal parts like pipes.
Both methods may be used in combination, depending on the risk assessment and regulatory guidelines.
Benefits of Cleaning in the Pharmaceutical Industry
Implementing a proper cleaning program provides several critical advantages:
1. Ensures Product Quality
- Prevents cross-contamination between batches.
- Maintains product purity and potency.
2. Regulatory Compliance
- Meets stringent GMP and regulatory requirements.
- Avoids penalties, recalls, or warning letters from regulatory bodies.
3. Protects Patient Safety
- Eliminates harmful residues and microorganisms that could affect patient health.
4. Operational Efficiency
- Reduces equipment downtime due to contamination.
- Improves the lifespan of manufacturing equipment.
5. Enhances Brand Reputation
- Consistently clean manufacturing areas reflect a company’s commitment to high standards and safety.
Conclusion
Cleaning is a non-negotiable process in the pharmaceutical industry that safeguards product quality, regulatory compliance, and patient safety. Companies must adopt effective cleaning procedures, regularly validate them, and ensure documentation to meet industry standards.